Innovation Demonstrators
Robots are becoming more and more important in the agricultural production process, taking over repetitive, risky, and time-consuming work from farmers and farm operators, while simultaneously increasing productivity and quality.
agROBOfood deployed the funding mechanism of Open Calls to support SMEs in their digitalisation journey. Through Innovation Experiments (IEs) SMEs managed to further mature the technologies needed to meet end user needs. The experiments were also used as an instrument to ensure the network’s interconnectivity and expansion of the service portfolio of DIHs with cutting-edge technological developments and novel breakthrough technologies.
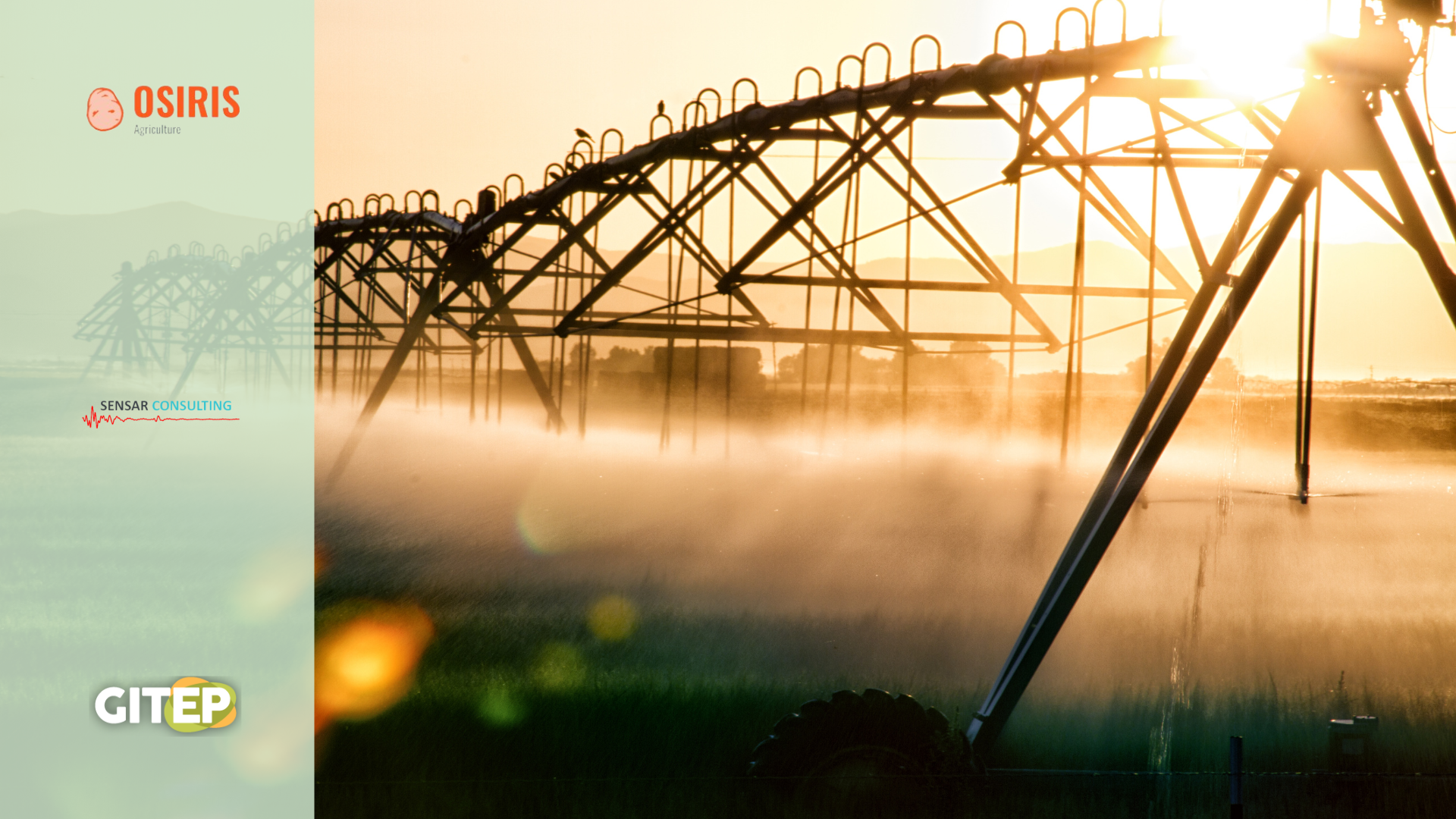
MIRAGE
DescriptionMIRAGE, a project developed by Osiris Agriculture in France, revolves around an automated robot armed with artificial intelligence for precise water irrigation in fields. The ultimate goal is to enhance water usage efficiency and relieve farmers from related manual tasks. Technical ProgressThe journey began with a prototype water irrigation system, "OSCAR" at a Technology Readiness Level (TRL) of 5. The aim within agROBOfood was to refine this system into a commercially viable product by boosting its efficiency and upgrading it based on farmers' feedback. A new prototype was completed during the development phase, integrating it with a ground-penetrating radar prototype inclusive of machine vision. This system was operational at the season's commencement, allowing extensive testing which led to several improvements. By the final report, the system had reached a TRL of 7, capable of performing water irrigation autonomously, receiving real-time data on water needs, and reducing water and energy consumption by 10% and 20% respectively. Further, it automated labour-intensive irrigation tasks, decreasing manual work by up to 80%. The use of ground-penetrating radar technology for soil moisture information collection could potentially lead to additional water savings of up to 45%. Network ProgressThroughout their agROBOfood participation, MIRAGE connected with two SMEs. A partnership with Sensar Consulting in Belgium provided them access to needed technology for their ground-penetrating radar technology. Further, they collaborated with GITEP80 in France, an end-user that provided a location for field tests and served as a demonstration point for connecting with other farmers. By the final report, MIRAGE had sold three robots as service contracts for 2024 and received fifteen letters of intent from interested farmers. They also engaged in talks with distributors in France, Belgium, Poland, and Switzerland, showcasing their efforts to broaden their market.To spread their results, MIRAGE participated in press articles, TV interviews, and attended a conference day organized by the Société Publique de Gestion de l'Eau. They also interacted with over 50 farmers at the Chambre de l'Agriculture de la Somme Conference and prepared a scientific journal article, "Ground-penetrating radar full-wave inversion for soil moisture mapping in trench-hill potato fields for precise irrigation". Lastly, they conducted demonstrations of their technology at several exhibitions and field days, and established contact with an irrigation machine reseller. Start Date: September 2021 Duration: 17 months Contact Person: Mr. Henri Desesquelles
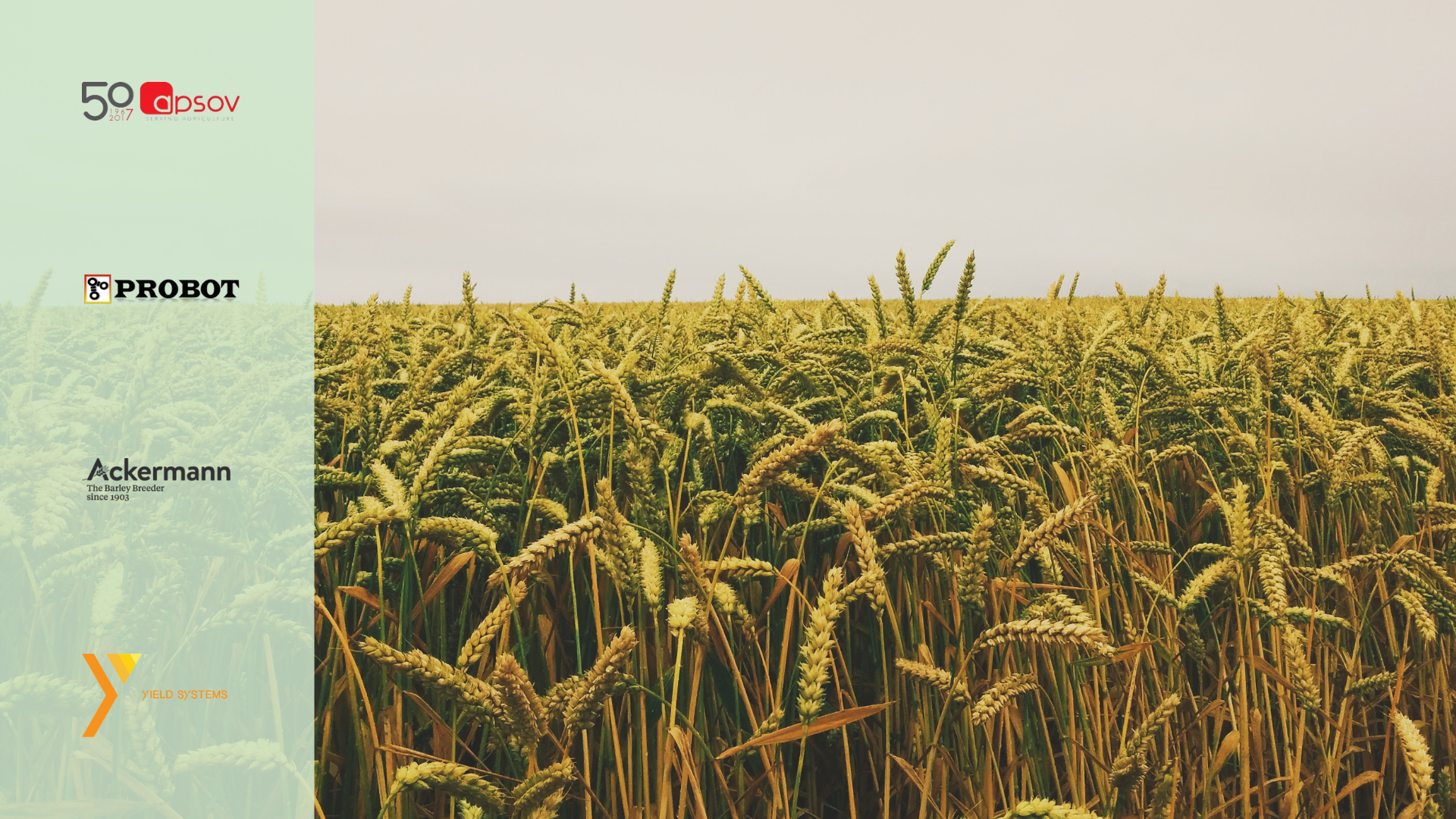
FullPheno
DescriptionFullPheno, a project by Yield Systems in Finland, is a software component designed for high-resolution canopy phenotyping. The software examines visual data captured by sensors and extracts crucial information about a crop's physical characteristics, thus providing insights into its growth, health, and performance.Technical ProgressThe project involved modifying the existing Yield System software to incorporate full canopy phenotyping capabilities. The software was also integrated with two field-capable rovers equipped with sensors and cameras. During the development phase, the software was enhanced with a Kubernetes-based video intelligence server to allow collaborators and customers to integrate and access phenotypic estimates. This software was integrated into an autonomous mobile robot designed for data collection in the field, serving as the foundation for the first robot designed for small-scale farming.Further modifications were made to the robot to meet user requirements. For instance, the length of the robot's linear unit was increased from 3 meters to 7.5 meters, allowing for greater coverage. The modified robot underwent simulation testing to ensure stability on uneven terrain, revealing the need for additional structural modifications. The robot was assembled at the laboratory of Probot Oy in Finland, where it was decided to upgrade the battery capacity by distributing the battery system across different areas of the robot. This revised system underwent successful outdoor and field tests.The Technology Readiness Level (TRL) progressed from 5 at the execution plan stage to 7 at both the development report and final report stages.Network ProgressUpon joining agROBOfood, FullPheno partnered with Ackermann Saatzucht GmbH & Co. KG in Germany, Probot Oy in Finland, and Apsovsementi S.P.A in Italy. They also utilized the services of their local DIH, LUKE Digilnno Services, consulting with LUKE experts and evaluating the robot concept during the planning phase. Field testing of the developed system was organized concurrently with the field-robot event in Ruukki, Finland, providing an opportunity to present the system to potential end users, including farmers and agricultural researchers.Their final report listed participation in various market activities and events in Asia, Europe, and the USA. During these events, they actively sought new potential customers by engaging in discussions with distributors. Yield Systems collaborated with Agricola2000 to offer trial services in their region, sharing the costs with trial service providers. Yield Systems has also been in discussions with more than fifteen investors since January 1, 2023, and participated in a prominent Nordic startup event in Finland, leading to over ten discussions with potential investors. The company is actively seeking new partners in crop insurance and is engaged in ongoing discussions with connections made at the events they attended. Start Date: September 2021 Duration: 17 months Contact Person: Mr. Jussi Gillberg
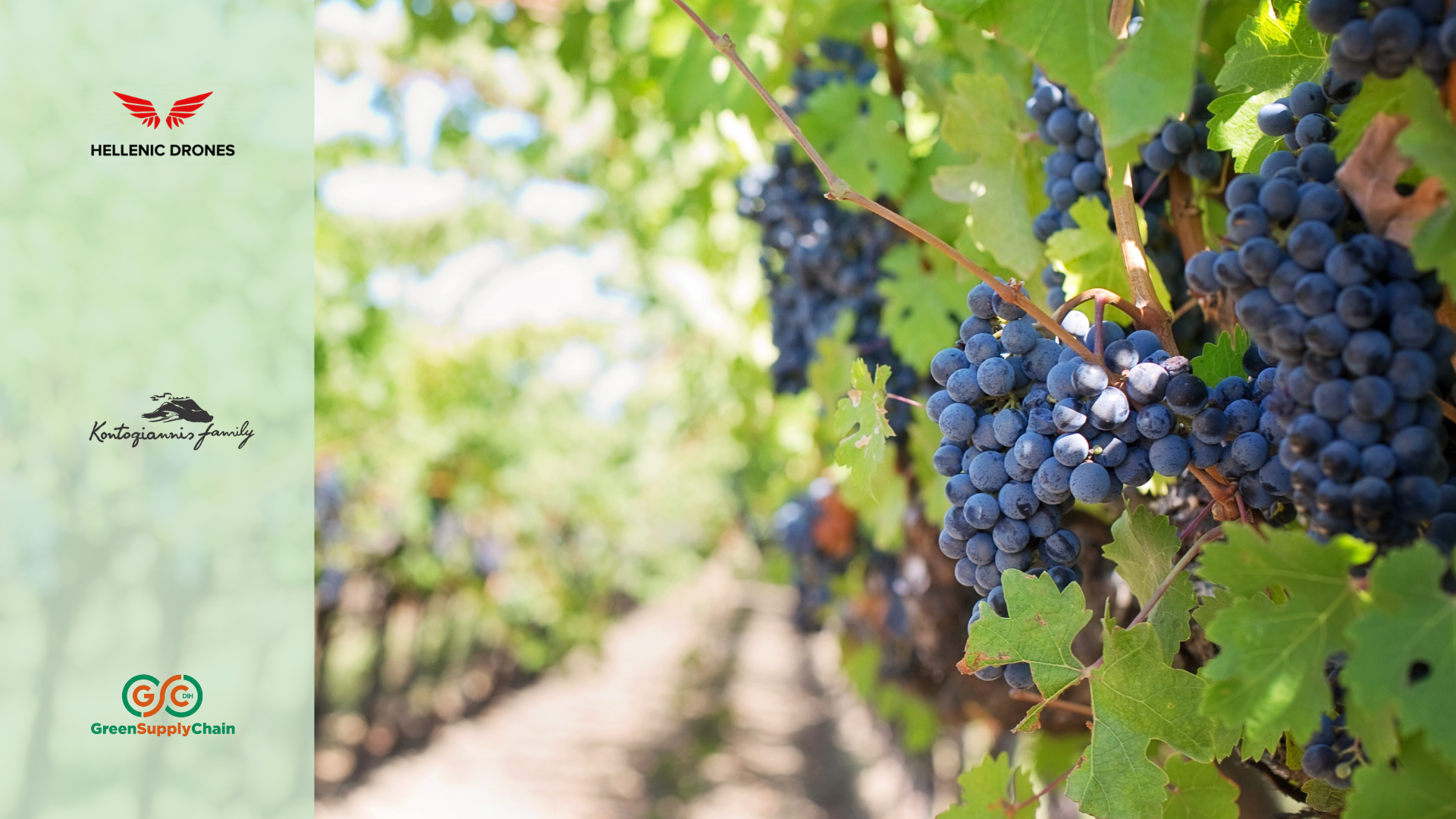
Oenobotics
DescriptionOenobotics developed by Hellenic Drones in Greece, offers a drone capable of autonomously scanning vineyards to provide early warning of downy mildew, powdery mildew, and water stress. The drone can also treat these issues, helping to reduce the use of pesticides, relieve workers of repetitive tasks, and ensure early detection of potential vine health issues.Technical ProgressThe project utilized a drone as a platform for development. The objective was to demonstrate the benefits and capabilities of an autonomous solution for real-time monitoring and targeted spraying in vineyards. The development phase saw the successful creation of an early warning system for detecting water stress and downy mildew, alongside the development of a deep learning model for processing images to detect changes in different vines.Additionally, the drone's capabilities were expanded to allow for a significant reduction in pesticide usage with autonomous navigation to affected areas in the vineyard. The drone was also equipped with the ability to autonomously land and recharge at a charging station.In the final report, the technical progress included the integration of a low-cost camera with plant disease and water stress diagnostic software, as well as a high-accuracy drone spraying system. The system's implementation demonstrated several positive outcomes, including a significant reduction in losses for wineries due to the avoidance of diseases or non-optimal conditions in vineyards.The Technology Readiness Level (TRL) progressed from 5 at the execution plan stage to 6 at both the development report and final report stages.Network ProgressionDuring the execution phase, partnerships were established with the Information & Communication Technologies Laboratory in Romania, Future Needs Management Consulting Ltd. in Cyprus, Green Supply Chain Digital in Greece, and an end user in Greece.In the final phase, the project organized various demonstration events where the system was showcased to young farmers. Additionally, 10 vine growers were supported in beta-testing the solution. A comprehensive analysis of the market landscape, trends, and projections for the future was conducted, helping to define the appropriate business model for the project. To reach and engage customers, the team created a website where they operate and present the latest developments and news about the product and upcoming events. Start Date: September 2021 Duration: 17 months Contact Person: Mr. Dimitrios Skilrios
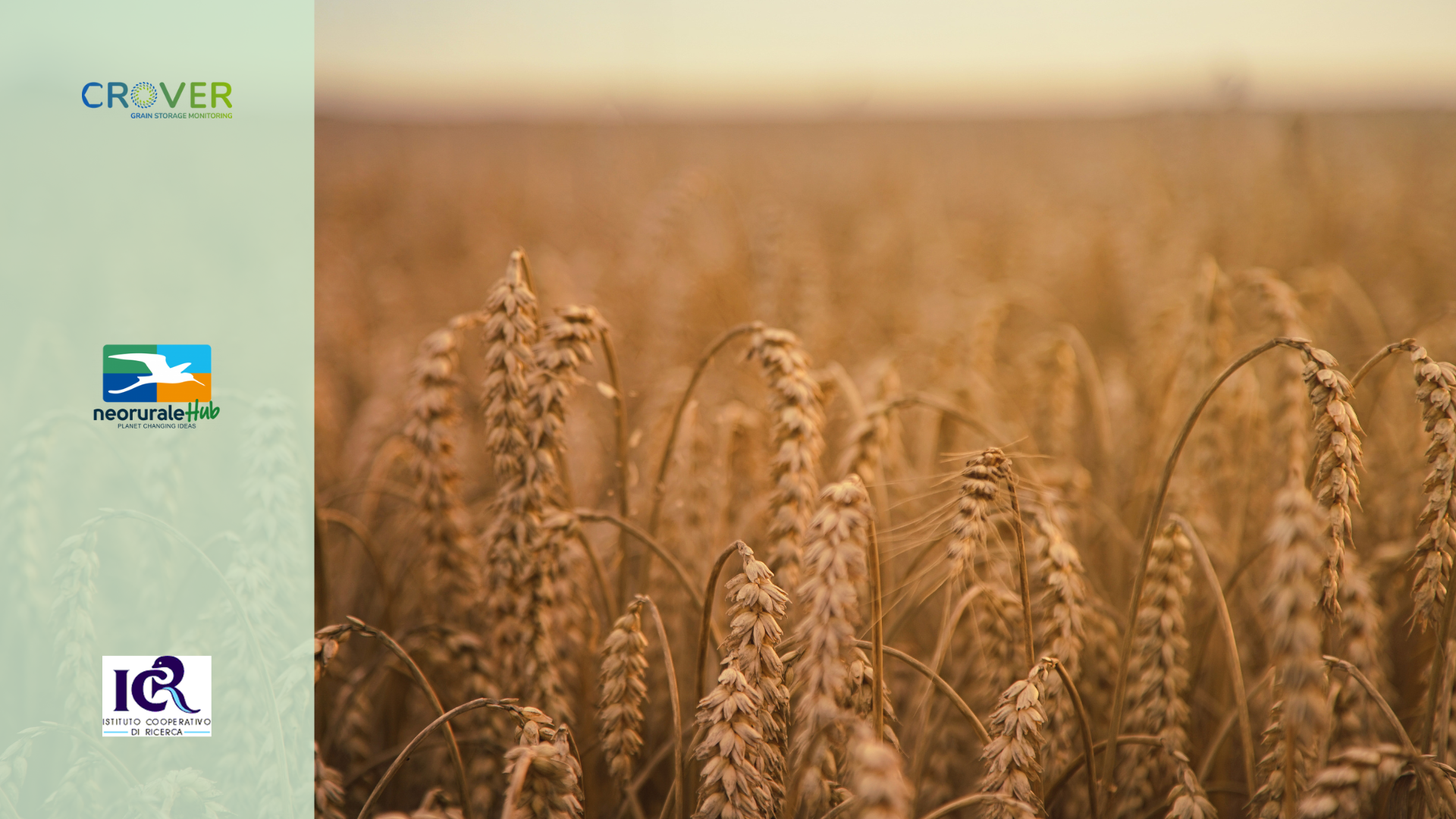
CROVER
DescriptionCROVER developed by CROVER TECH in Scotland, offers a burrowing drone capable of autonomously scanning and sampling grains in bulk storage. This technology provides early detection of potential spoilage, improving the quality control of grains in bulk storage, enhancing the safety and handling of quality control for storage operators, and relieving them from performing quality assurance tasks inside bulk storage. Technical ProgressThe project began with an existing drone designed for autonomously scanning and sampling grains in bulk storage while swimming through them. The objective was to conduct iterative tests and trials in an operational environment, specifically flat grain storage. The initial tests aimed to assess the system's performance and identify areas for improvement.During the development phase, the project planned and executed an extensive tour, conducting tests and experiments at potential storage sites in both the UK and Italy. These tests provided valuable insights and crucial information for optimizing the system's capabilities. Based on the feedback and information gathered, the project made improvements and modifications to the system which included developing a non-interfering system that monitors storage operations and can be adapted to diverse storage environments, while also adhering to industrial standards.The system was also tested with different crops, providing valuable insights. It was observed that paddy rice posed challenges for the system, while soybeans and peas were more approachable, indicating wider potential markets in terms of crop coverage.From the final report, the project's technical progress with the latest improvements has pushed the system to a desired Technology Readiness Level (TRL) of 8. CROVER now has a minimum viable product (MVP) ready for the necessary certification before being manufactured at small scale and launched on the market.Network ProgressionUpon entering the project, the team established contact with two end users: NeoruraleHub s.r.l. and Istituto Cooperativo di Ricerca, both located in Italy. According to the final report, the project successfully implemented their solution at four different test locations, two in Scotland and two in Italy, with Istituto Cooperativo di Ricerca being one of them.During the development phase, the project greatly benefited from testing and trials conducted with end users, which provided valuable insights for optimizing and improving the system's capabilities.For dissemination activities, the project participated in various events, including Youth Outreach, World Agri-Tech Innovation Summit, EIMA International, Agriscot, and the Scotsman GreenSkill Conference. The main demonstration took place at Stoccaggio 4.0: La filiera ceralicola del futuro, in a two-day event. On the first day, the project interacted with 10 local rice producers, and on the second day, they engaged with 30 members of the farming association. The demonstration was also covered in a press publication. Start Date: September 2021 Duration: 17 months Contact Person: Mr. Lorenzo Conti
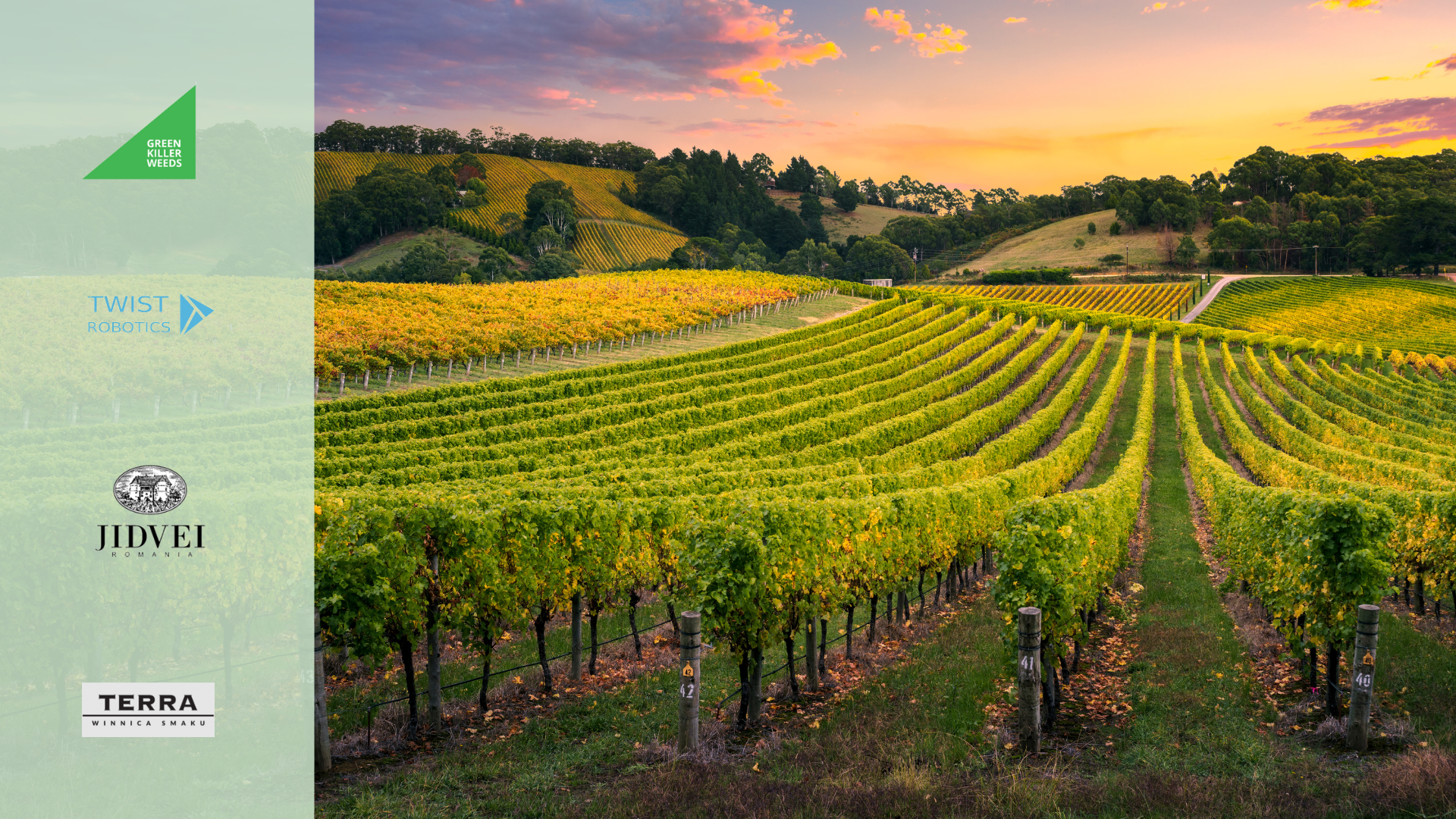
ZEROTOXVINE
DescriptionZEROTOXVINE developed by GreenKillerWeeds S.L in Spain, offers an autonomous weed removal cell mounted on a tractor. Capable of detecting and removing weeds using microwave technology, this system aims to reduce pesticide use and enable weed removal for organic farming. Technical ProgressAt the project's outset, the innovation experiment had a validated sensor head in a laboratory environment. The aim within the agROBOfood project was to develop a complete system prototype, which included a sensor head, console operator, weed elimination head, and the necessary artificial intelligence and machine learning software. The goal was to enable the system to autonomously remove weeds.During the development phase, the project successfully completed various activities. They defined requirements based on feedback from end-users and constructed the ZEROTOXVINE robot using existing market hardware. The robot was then adapted to effectively remove weeds. The complete system underwent testing at two different end-users' vineyards, which provided valuable feedback for further improvements. The testing yielded satisfactory results, particularly in using a lateral hydraulic arm with a microwave head to target and remove weeds between the vine rows. This approach demonstrated an average efficiency of 60% in weed recognition and removal. The system performed best at lower speeds, indicating optimal working conditions.From the final report, the design and assembly of the system have been completed and successfully tested. The automation of weed recognition and removal showed an average efficiency of 60%, with the best results achieved at lower speeds. The project made significant technical progress by developing and testing a complete system prototype for autonomous weed removal.The Technology Readiness Level (TRL) progressed from 4 at the execution plan stage to 4 at the development report stage, and finally reached 6 at the final report stage.Network ProgressionUpon entering the project, the team established contact with two vineyard end users, SC Maria Turism SRL - Jidvei in Romania, and Dekanter Sp. Zoo - Terra Winnica Smaky in Poland. These partnerships were instrumental in facilitating the testing of the system within the vineyard environments.In terms of dissemination, the project team organized demonstration days at the premises of both end users. These events aimed to generate interest from potential end users and gather valuable feedback on the complete system. The demonstrations provided an opportunity for interested parties to witness the capabilities of the system first-hand. Furthermore, the project team utilized social networks such as Facebook and LinkedIn as platforms for dissemination. These channels were leveraged to attract potential customers and investors, expanding the reach of the project, and generating awareness of their innovative solution. Start Date: September 2021 Duration: 17 months Contact Person: Mr. Carles Arnabat
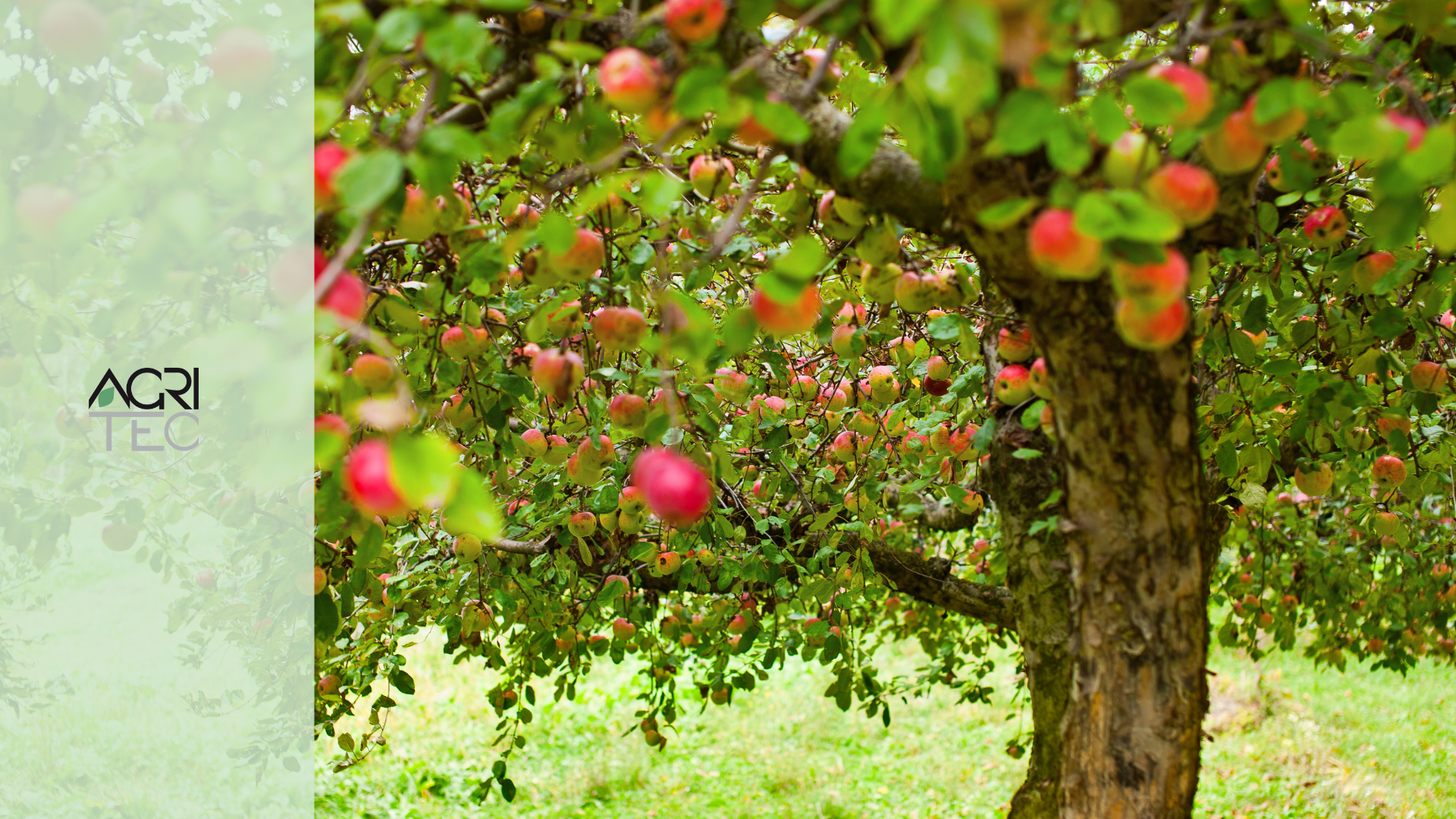
TOMMIE
DescriptionTOMMIE developed by Aigritec S.r.l. in Italy, is a novel robot designed for chemical blossom thinning. This robot applies chemicals directly onto the flowers in specific targeted locations and dosages, tailored to each plant. The aim of this technology is to relieve workers from repetitive and laborious tasks, monitor apple tree flowers, achieve optimal thinning rates in highly variable environments, and decrease the use of chemicals. Technical ProgressThe TOMMIE experiment developed a robot capable of aiming and spraying micro dosages of liquid. The initial objective was to finalize the system design, which underwent significant technical upgrades compared to the original prototype. The team successfully completed a flower detection system, including a GUI for monitoring and scanning orchard flowers. This system was installed on a portal device used in the field. Challenges encountered during the testing of the sprayer's nozzle and arm were resolved by finding an optimal configuration.The Technology Readiness Level (TRL) progressed from 5 at the execution plan stage to 6 at the development report, and finally reached 7 at the final report.Network ProgressionDuring the development phase, Aigritec established a collaboration with F.lli Rabbiosi, one of the largest apple farming companies in South Tyrol, which was crucial for validating the technology. Additionally, Aigritec connected with the Laimburg Research Centre, South Tyrol, to test and evaluate their system's performance against traditional methods in a dedicated orchard.Aigritec's robust network of end users includes all the major players in the South Tyrol and Trentino regions, such as VOG, VIP, and Marlene. This potentially gives Aigritec access to 50% of Italy’s apple production and 15% of Europe's apple production. Ongoing discussions with potential investors are also taking place, with several considering investment once the robot receives CE marking, validation, and makes its initial entry into the market. Start Date: May 2021 Duration: 17 months Contact Person: Dr. Elia Bruni
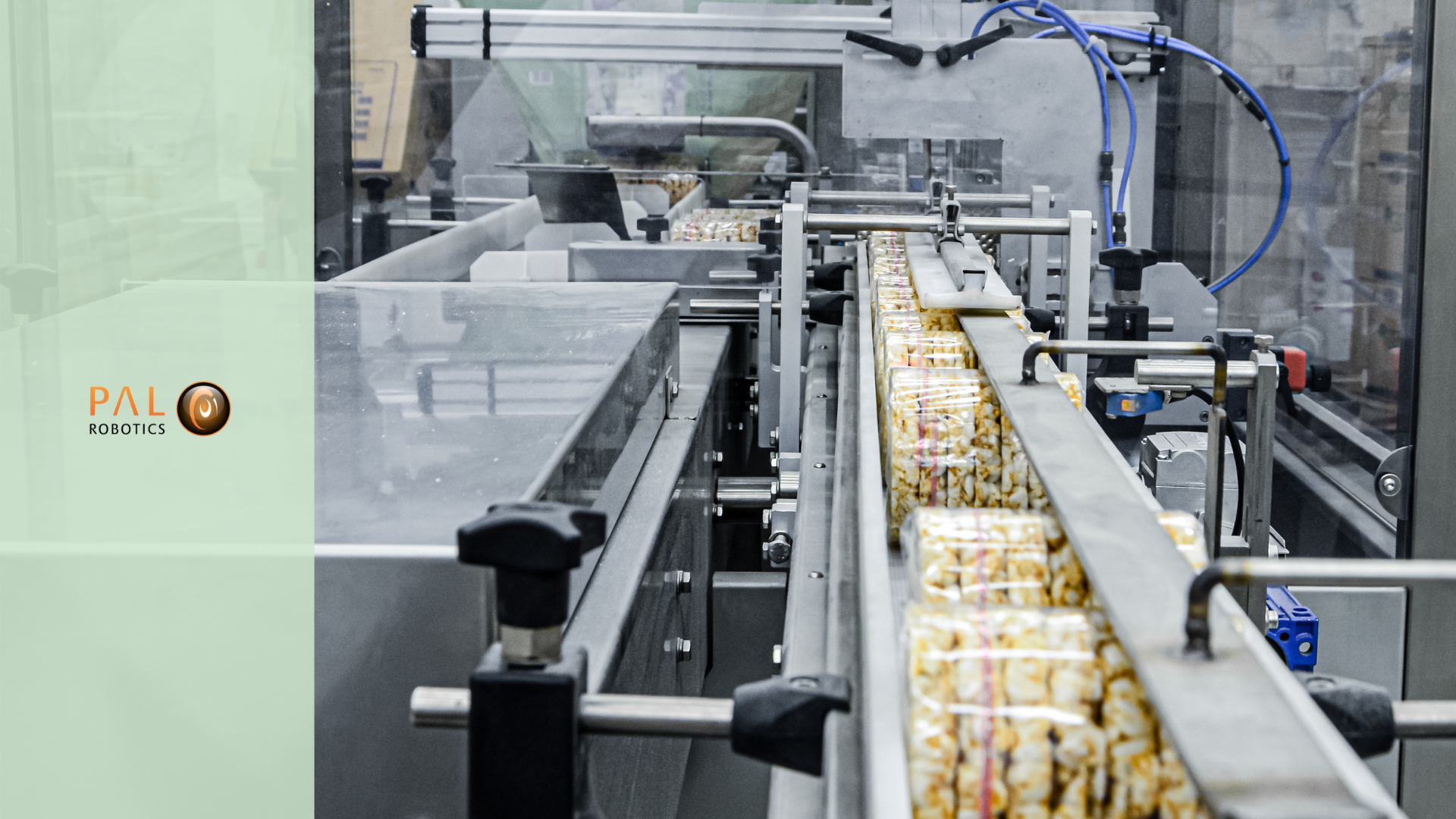
SCaFo
DescriptionScaFo developed by PAL Robotics in Spain, aims to create an Autonomous Mobile Robot (AMR) designed specifically for the food industry. The robot is built to withstand low temperatures, high humidity, and slippery floors, and can transport processed food. It can also be equipped with a manipulator for handling food. This technology aims to relieve workers from repetitive food handling and transportation tasks and improve the labour force workflow and workload.Technical ProgressThe ScaFo experiment is an improvement on an existing solution from PAL Robotics, with the goal of making the robot's base design more robust for operation in the food industry. Significant effort during the development phase resulted in technical progress, including the definition of scenario and robot tasks, design of a transportation structure for the robotic platform based on modularity, and improvements in the current design's ergonomics and connectivity.Further work detailed in the final report resulted in numerous final hardware designs. The base design now complies with regulations, using materials compatible with the food industry. A new suspension concept was adopted, cushioned caster wheels and covers were designed with manufacturing in mind, and all electronic components are commercial and approved. Software development optimized the mobile robot's navigation and human-aware navigation, further developed fleet management, task scheduler, and visual programming of tasks, and conducted integration and testing. Pilot tests at General Cárnia successfully validated the core functionalities of the robotic solution in a real food industry setting. The final Technology Readiness Level (TRL) progressed to 7.Network ProgressionPAL Robotics initially sought potential end-users and interest groups for the project. This search resulted in a confirmed end-user, the General Cárnia factory in Barcelona, which provided an actual test environment and helped validate the potential of the solution. This collaboration led to new contacts and partnerships with potential customers, provided valuable feedback on the robotic platform's functionality and user acceptance, and gave necessary insights to further mature the solution towards commercialization. Dissemination of the project has been mainly through social media, where several posts and updates on the solution progress have been posted. The social media platforms used for advertising include Facebook, X (former Twitter), LinkedIn, and press releases. The project has also been mentioned at physical events. Start Date: May 2021 Duration: 17 months Contact Person: Mr. Francesco Ferro
All robotic experiments conducted within the agROBOfood network that used its internal resources, are mapped above. The aspiration is that those can help raise awareness on technologies that are already commercially available and those expected to become market-ready over the next two to three years, as well as increase cross-border collaboration and boost market expansion.
New combinations of enabling technologies with robotics, data gathering and AI-driven decision making, create new opportunities for markets and novel agri-food systems that can transition from a pilot state to market-ready product.
Open Calls
agROBOfood Innovation Experiments (IEs) were initiated to address pressing agricultural needs identified by the industry. Open Calls were used as a tool to financially support agri-food SMEs and ensure the smooth-running digital transformation of their processes. SMEs that were selected through the calls and received tailored on-demand technical and business services from the (mentor) DIHs of the network. Moreover, through their participation, they gained EU-wide visibility, attracted investors and explored funding opportunities.
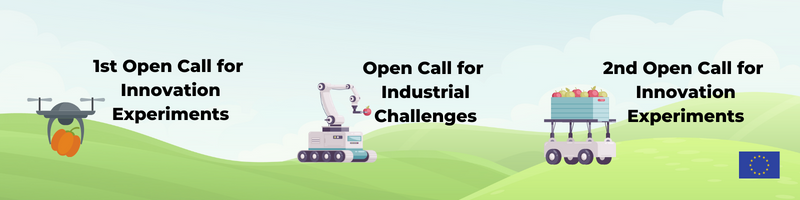

This process enabled the agROBOfood network to develop and test its service offerings under real conditions, although COVID-19 travel restrictions compromised the development of a network portfolio of cross-border services
Besides mobilising EU funds and facilitating the provision of scale-up/ acceleration services, this mechanism set the foundations for DIH to SME enhanced collaboration and boosted the network’s expansion. Ultimately, the mechanism of Open Calls created a roadmap to help DIHs engage with SMEs and industry, support the innovation support system at a regional level and boost the maturing process of providers.
In total there were 3 Open Calls that attracted 231 applications. Along with agROBOfood DIHs were able to improve the quality of the services provided, identifying missing services and offering new ones based on demand. The network’s added value is that it takes a complex innovation ecosystem and simplifies it, offering valuable services at the fingertips of its users.
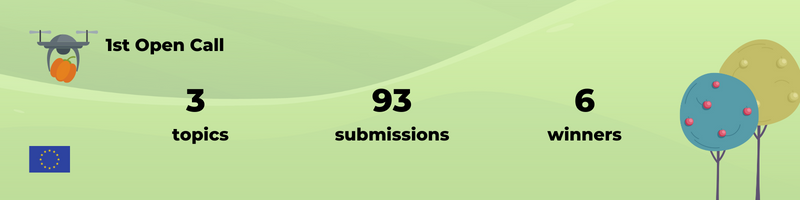

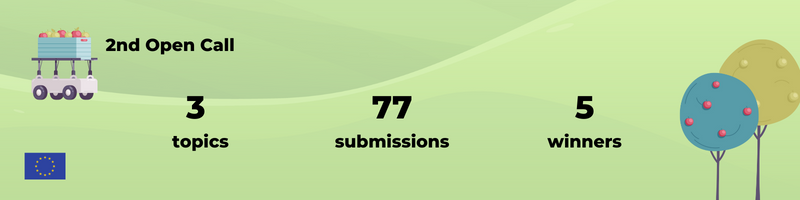
agROBOfood’s innovation support system, helps and guides SMEs to easily identify who to work with or to approach for assistance in the design of a service or the integration of robotic solutions. The most under-appreciated reason that digital transformations often fail is by going too big, too fast. There’s a learning curve to digital transformation, and most SMEs need to walk before they can run. The key is to advise SMEs to start with modernization efforts that don’t transform the business—much less create a new one—but which create the capacity to succeed in more ambitious efforts later on.
Finally, through dissemination of the results, best practices and benefits of the experiments within the ecosystem, DIHs manage to raise awareness about the opportunities found at the nexus of robotics and agriculture.